M-Jet Devices
High-performance systems for your industrial safety needs
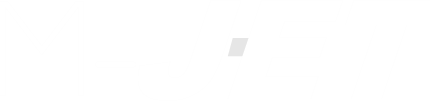
M-JET is the world’s most advanced hazard monitoring system. It will ensure complete control and real-time data that is necessary to avoid unnecessary maintenance and explosion hazards.
breadcrumb >> list
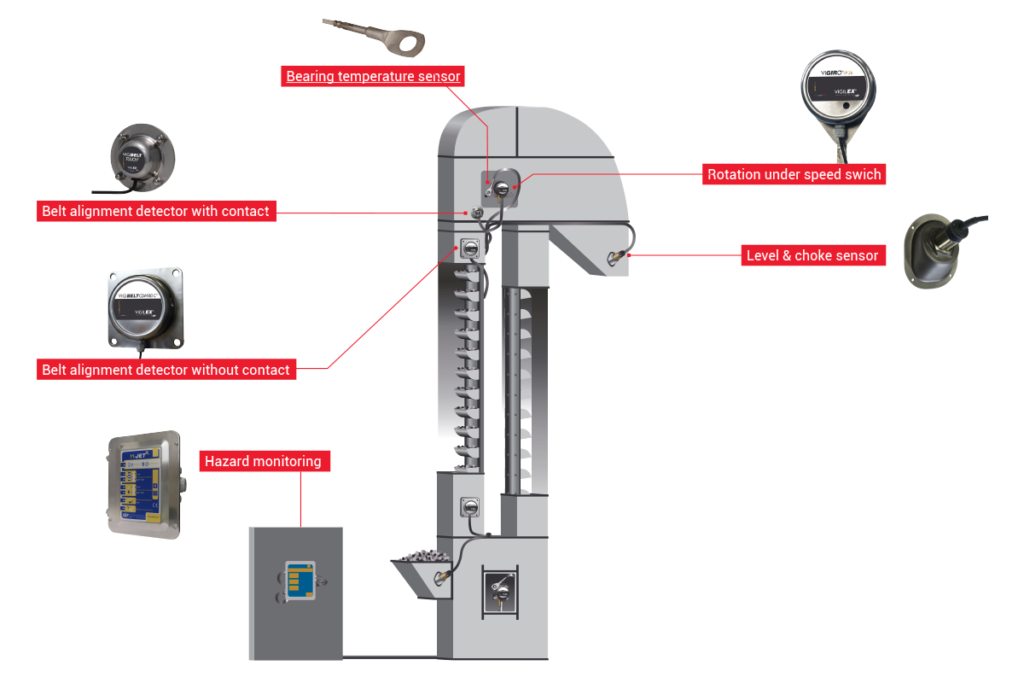
M-Jet Grain Elevator Hazard Monitoring Devices
M-JET, the world’s most advanced hazard monitoring devices, ensures complete control and real time data that is necessary to avoid unnecessary maintenance and explosion hazard. The hazard monitoring devices are able to monitor bucket elevators, belt conveyors, chain conveyors and screw conveyors, analyzing the data sent by the sensors installed on equipment and saving the eventual defects events
Data Reports include dangers associated with speed control, misalignment, level & choke control, bearing and motor temperatures. M-JET SYSTEMS is specifically designed as an early warning system to alert facilities to potential sources of explosion ignition. According to the setting, the system sends alarms and commands the stopping of the conveyor.
The smart way to manage your conveyor systems
- Under speed due to belt slip on the pulley. To check comparing with the nominal speed.
- Bearing temperature using sensor PT100 or NTC.
- Belt misalignment using sensors with or without contact.
- Material jam in conveyor entry or exit using capacitive sensor.
- Chain elongation measured by inductive sensor and targets.
- Motor power measurement with specific electrical consumption.
- Shaft position measured by sensor 4-20mA.
The operating control of the system is achieved by output relays
- Directly on the power relay of the motor.
- By the global PLC of the facilities.
Verifying the conveyor operation can be achieved by:
- On computer screen by internal website (directly with laptop or by Network LAN).
- By message on the email box (events and maintenance operation plan).
M-JET systems electronic connectivity via internet or facility network
- Remote monitoring up to 120 conveyors from the same display unit
- Unified viewing of data in real time
- Graphic display of historical data
- Viewing of alarms
- Alarm notification by sending email
- Support tools to manage preventive maintenance
Historic data analysis
- Only by computer, directly with laptop or by Network LAN
- History of defects: M-JET SYSTEMS can save 10,000 events
- History of setting modification: Save the 10,000 last setting modifications
- History of daily running time of the equipment:
– M-JET SYSTEMS saves production time during the last 4,000 days of use
– M-JET SYSTEMS records temperatures 24 times per day during the last 365 days of use - All the history can be downloaded in csv format
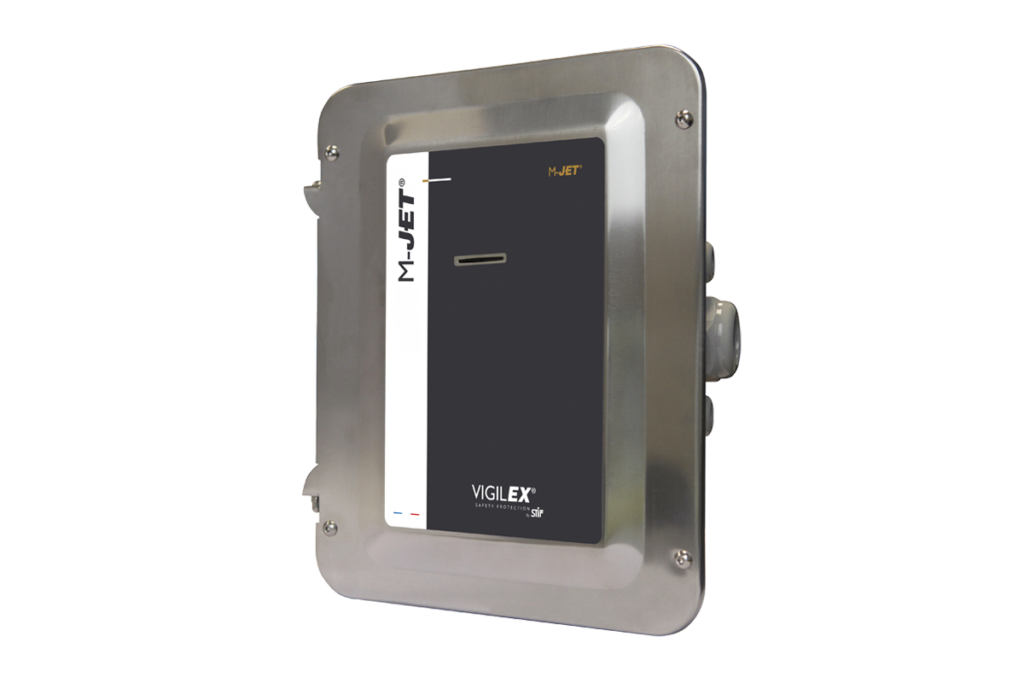
M-Jet
Hazard Monitoring System Without Display
Design Features
- Strong casing.
- Dustproof and waterproof casing.
- Remote management use.
Sensors Supervised by the M-Jet
- 2 belt speed sensors.
- 2 choke and level sensors.
- 2 follower shaft position sensors.
- 5 bearing temperature sensors.
- 2 chain elongation sensors.
- 3 analogic sensor
- 4 belt alignment sensors.
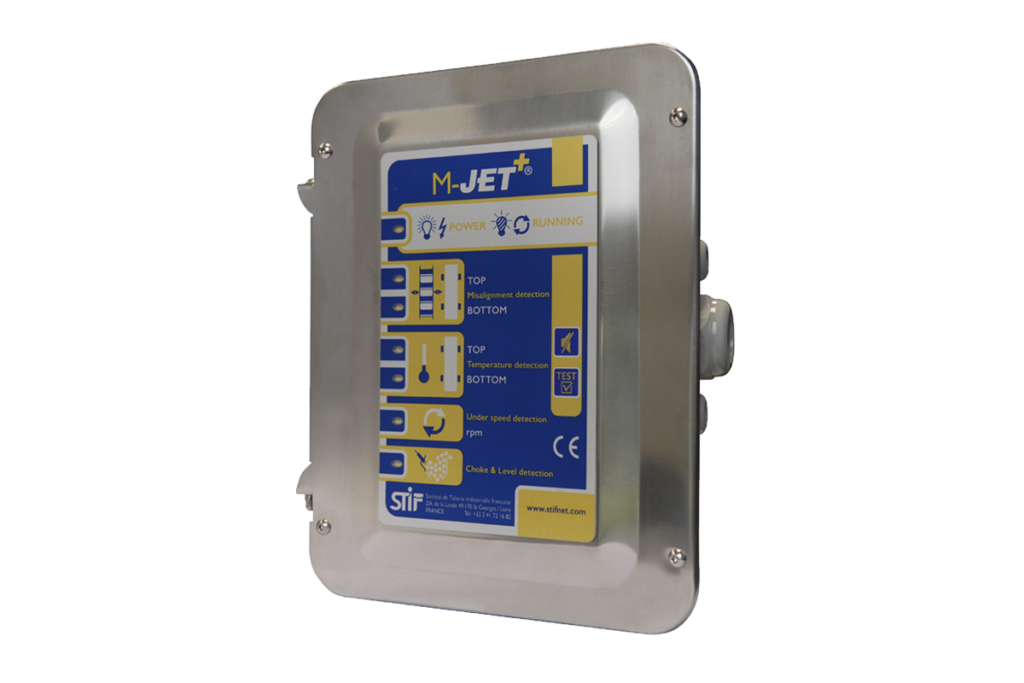
M-Jet +
Hazard Monitoring System With Display
Design Features
- Strong casing.
- Dashboard with LED indicator.
- Dustproof and waterproof casing.
- Work stand by the conveyor.
- Running status indicator near the conveyor (and sound alarm).
Sensors Supervised by the M-Jet +
- 2 belt speed sensors.
- 2 chain elongation sensors.
- 4 belt alignment sensors.
- 3 analogic sensor.
- 2 follower shaft position sensors.
- 2 choke and level sensors.
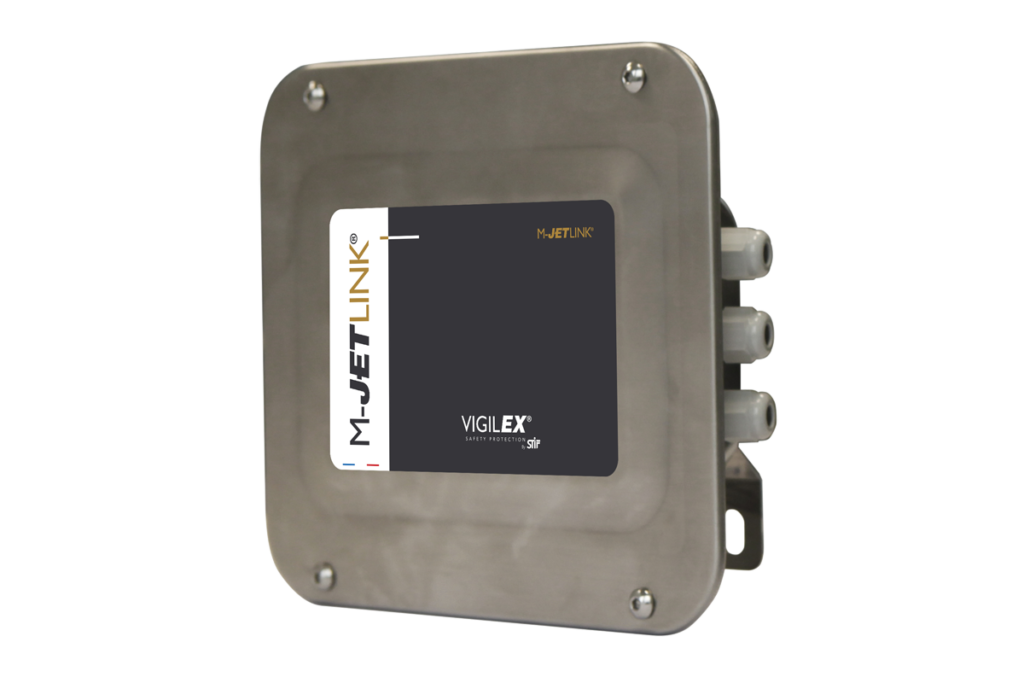
M-Jet Link
Hazard Monitoring System Without Display / Accessories
Connection Box
- The BURST SENSOR is a very efficient element to inform when your safety devices are open. Get the signal in real time and increase the safety of your facilities.
- Help to connect sensors on Master M-JET+ or M-JET for only one conveyor, by extension wire (multicables).
- Connection box to add for conveyor length between 20 meters and 80 meters
How the M-Jet Hazard Monitoring System works
The M-JET hazard monitoring system analyzes data that is transmitted from multiple sensors installed on the conveyor equipment. When wear points and hot spots are detected an alert is sent, signaling the need for necessary maintenance. This early warning capability greatly reduces the need for costly equipment replacement and explosion hazard potential.
M-Jet and M-Jet+ Systems
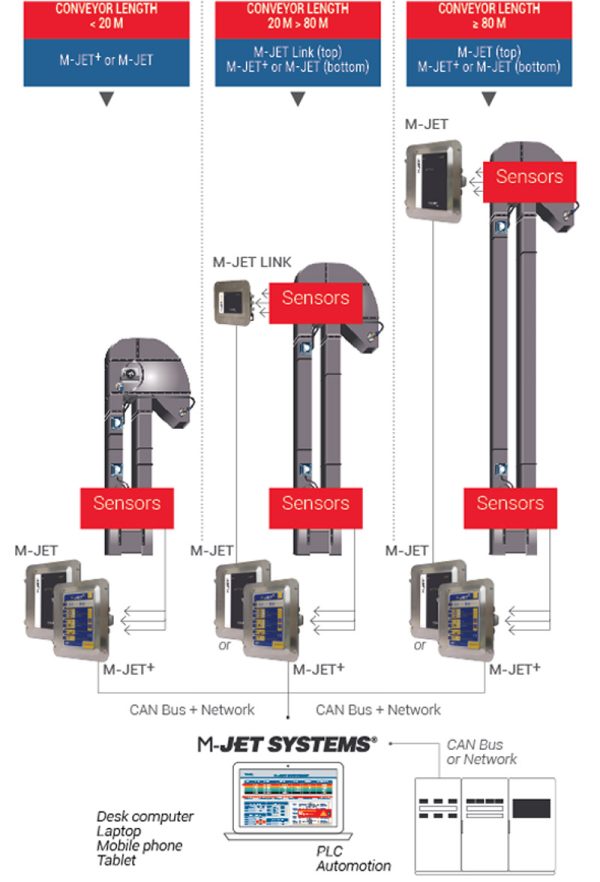
M-Jet Link Connection Box
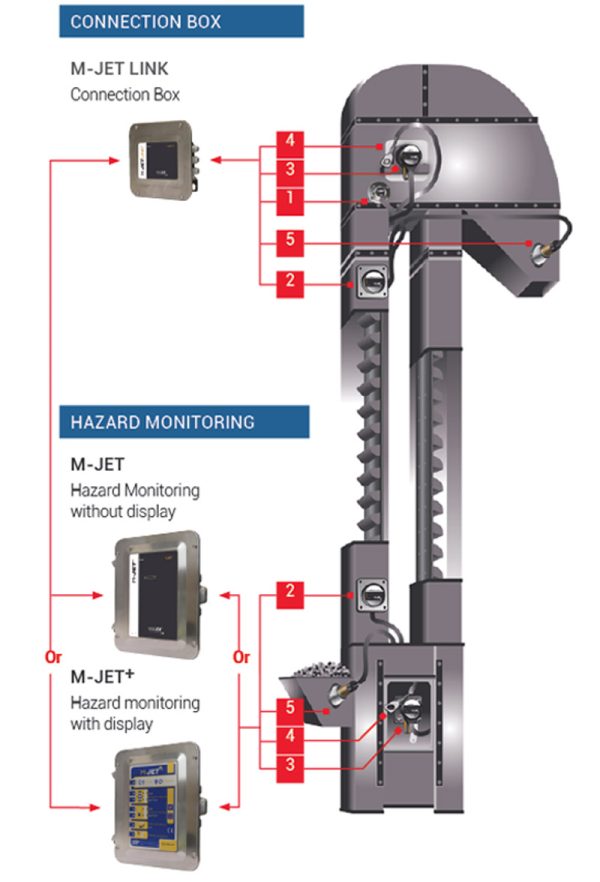