Optimizing Material Handling: The Advantages of Custom-Built Pneumatic Conveyors
breadcrumb >> list
Custom-Built Pneumatic Conveyors
Pneumatic conveying systems utilize air pressure to transport materials through pipelines in precisely measured and timed quantities. They have become integral to industrial material handling. These systems offer a precise, clean, safe, and efficient way to move bulk materials like powders, granules, and even bulkier materials, reducing contamination and enhancing operational safety. While standard configurations serve most needs, the unique demands of specific industrial processes often require custom-built solutions. Customized pneumatic conveyors are tailored to meet specific operational requirements, accommodating unique plant layouts, specific material characteristics, and integration with advanced monitoring systems. This article delves into the mechanics of pneumatic conveyors, highlights the advantages of customization, and offers guidance for those considering integrating an pneumatic conveyor into their existing applications.
Understanding Pneumatic Conveyors
Understanding the versatility of these systems and their applications across different industries is essential for selecting the right type of pneumatic conveyor—this ensures the system not only fits the facility’s physical layout but also enhances operational efficiency and safety, meeting the specific needs of various industrial processes.
Types of Pneumatic Conveyors
There are primarily two types of pneumatic conveyors, each suited to different material characteristics and handling needs:
Dilute Phase Conveying
- Characteristics: This method suspends materials in the air stream as they move through the pipeline. It is generally used for lighter, non-abrasive materials.
- Applications: Ideal for transporting food products, chemicals, and small, light materials that can easily be suspended in air.
Dense Phase Conveying
- Characteristics: In this type, materials are pushed or pulled along the bottom of the pipeline, suitable for abrasive or very fragile materials.
- Applications: Best for handling robust materials like sand, metal powders, or chemicals that require gentle handling to prevent degradation.
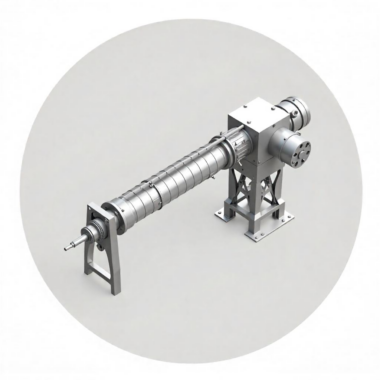
Industry-Specific Applications
Pneumatic conveyors are not just limited to granular or powdered materials; they also play a crucial role in industries handling other forms of bulk materials:
Textiles: In the textile industry, these systems manage fibrous waste, transporting it from production areas to waste collection sites, thus maintaining cleanliness and reducing manual waste handling.
Laundry Facilities: Large-scale or industrial laundry operations use pneumatic systems to move soiled linens and garments from receiving areas to washers, and clean items to folding or sorting areas. This reduces labour costs, improves operational efficiency, and helps maintain high hygiene standards by minimizing physical contact with contaminated laundry.
Pharmaceuticals: In pharmaceutical manufacturing, pneumatic conveyors transport bulk drug powders, granules, and capsules through various production stages. They maintain a contained environment to prevent cross-contamination and protect sensitive materials, ensuring adherence to strict hygiene and safety standards.
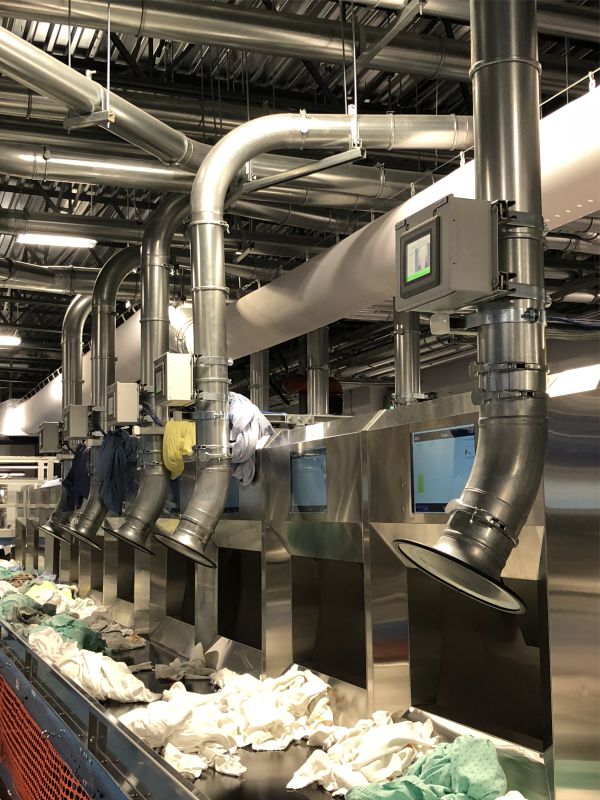
The Case for Customization
In the diverse landscape of industrial applications, one-size-fits-all solutions often fall short of meeting the specific requirements of different materials, processes, and environmental conditions. Custom-built pneumatic conveying systems provide a solution, tailoring each aspect of the conveyor to the unique needs of the facility and the materials it handles. This section explores the compelling benefits of opting for a customized pneumatic conveyor system.
Enhanced Efficiency and Productivity
Custom-built systems are designed to optimize the conveying process by matching the system’s capabilities to the specific properties of the materials being transported. This includes consideration for the material’s abrasiveness, moisture content, and particle size, ensuring minimal wear and tear on the system and reduced downtime for maintenance. Additionally, these systems can be engineered to fit into existing spaces and workflows, maximizing space utilization and enhancing overall process flow.
Reduced Operational Costs
Customization allows for the integration of energy-efficient components and design choices that align with the operational goals of the facility. By optimizing the air supply, pipe routing, and material feed mechanisms, a custom-built system can significantly reduce energy consumption and operational costs over time. Moreover, the precise control over material flow reduces waste and improves material handling efficiency, further driving down costs.<
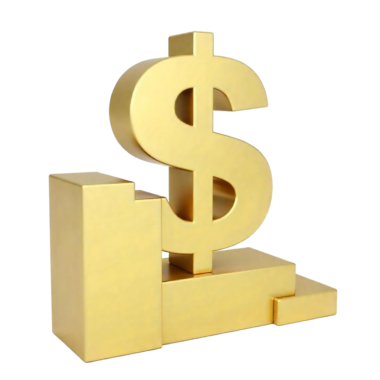
Increased Safety and Compliance
Each industry has its regulatory requirements and safety standards. Custom-built pneumatic conveyors can address specific hazards associated with different materials, such as explosive dust or harmful chemicals. Systems can be designed with built-in safety features that control dust emissions, reduce fire risks, and ensure the system complies with local and international safety standards.
Long-Term Reliability and Scalability
Customization not only addresses current needs but also allows for future modifications and expansions. As business needs evolve and production scales, custom systems can be adapted or expanded with minimal disruption. This foresight in design ensures that the pneumatic conveying system remains a reliable component of the facility’s operations, capable of adapting to changing demands.
Specialized Handling for Sensitive Materials
Certain materials require specialized handling to maintain integrity or prevent degradation during transport. Custom pneumatic systems can be designed with features like gentle handling modes, controlled environments, and specific material pathways that minimize breakage and preserve the quality of delicate or highly reactive materials.
By investing in a custom-built pneumatic conveyor, industries can achieve a perfect alignment between their material handling requirements and their operational objectives, leading to improved efficiency, safety, and profitability. This strategic approach not only optimizes immediate handling needs but also provides a scalable solution that grows with the business.
Key Considerations for Customization
Customizing a pneumatic conveying system requires a thoughtful assessment of several critical factors to ensure the setup not only meets current needs but is also adaptable for future requirements. This section outlines the primary considerations industrial purchasers and engineers should evaluate when designing a custom pneumatic conveyor.
By taking these factors into account, a customized pneumatic conveying system can be developed to deliver optimal performance, safety, and compliance, ensuring long-term reliability and efficiency in the industrial environment.
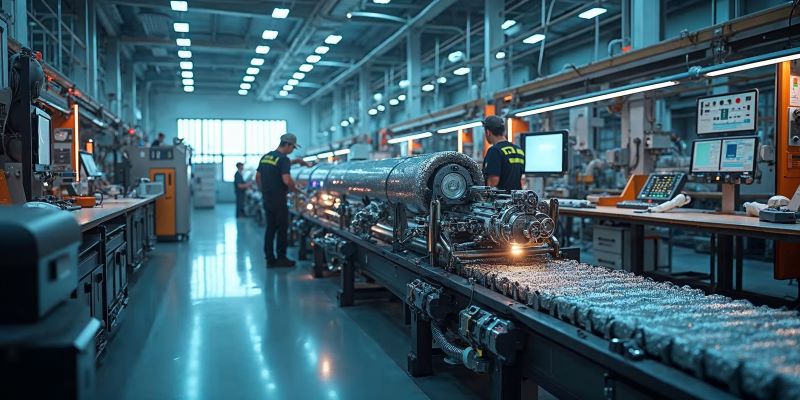
Material
Characteristics
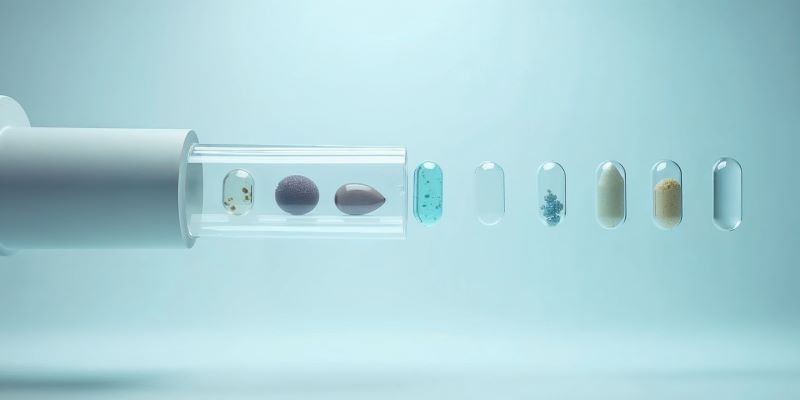
The physical and chemical properties of the materials being handled play a pivotal role in system design:
- Particle Size and Distribution: Different sizes and distributions can affect the flow characteristics and system efficiency.
- Abrasive Nature: More abrasive materials necessitate the use of wear-resistant materials in system components to reduce maintenance.
- Moisture Content: High moisture content may require systems that prevent material clumping and pipeline blockages.
- Chemical Properties: Reactive or corrosive materials need compatible materials for all system parts that come into contact with the product.
Facility Layout Considerations
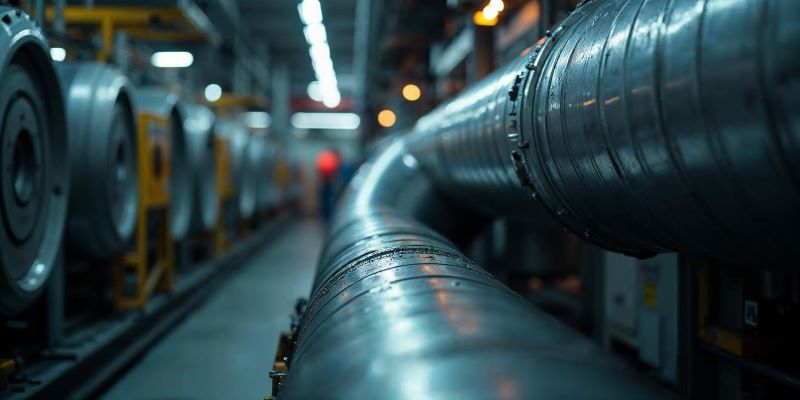
The physical layout of the facility can greatly influence the design of a pneumatic conveying system:
- Space Constraints: The available space dictates the system’s configuration and the placement of its components.
- Integration with Existing Systems: A custom system must be compatible with existing production lines and equipment.
- Routing and Accessibility: Efficient routing minimizes energy consumption and facilitates maintenance and expansion.
Environmental and Safety Considerations
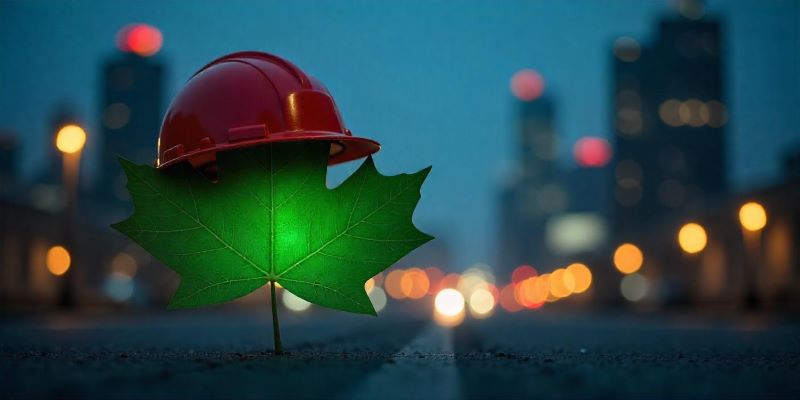
Safety is paramount, especially when handling potentially hazardous materials:
- Dust Control: Effective dust management systems are crucial to prevent air quality issues and reduce explosion risks.
- Explosion Protection: Systems handling combustible materials must incorporate features that mitigate explosion risks, such as grounding, venting, and suppression systems.
- Regulatory Compliance: The system must adhere to local and international safety standards, which may dictate certain design and operational parameters.
Design Elements of Custom-Built Pneumatic Conveyors
When it comes to custom-built pneumatic conveyors, every design element is tailored to maximise efficiency, adaptability, and safety in industrial settings. This section delves into the critical components and innovations that define these specialised systems.
By focusing on these design elements and innovations, custom-built pneumatic conveyors can significantly improve the efficiency, safety, and sustainability of material handling processes. Tailored solutions not only meet the specific needs of different industries but also adapt to the evolving demands of production environments, ensuring long-term reliability and cost-effectiveness.
Engineering Design Aspects
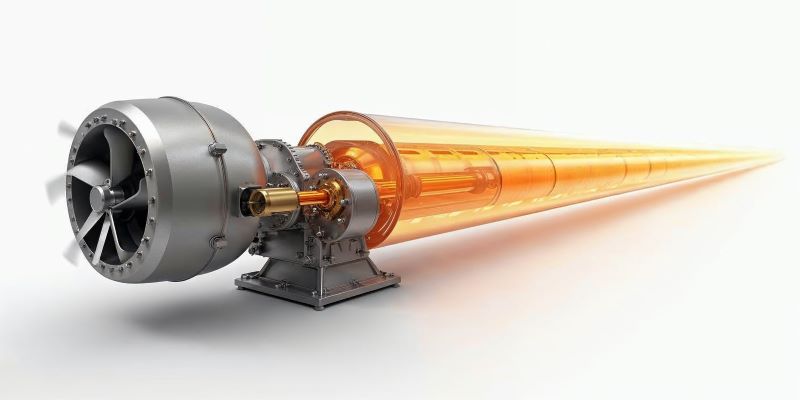
- Air Mover: The heart of any pneumatic system, the air mover, typically a blower or compressor, is selected based on the required air volume and pressure to efficiently transport materials. Custom solutions might incorporate energy-efficient models to reduce operational costs.
- Airlock: Essential for maintaining pressure and efficiency in the system, airlocks prevent air leakage at the feed point while allowing solid material to enter the pneumatic system. Designs are customised to handle different material volumes and types, improving system performance.
- Conveyor Line: Custom configurations of the conveyor line, including the diameter and layout of the pipes, are critical. These are designed to minimise wear and energy use, particularly when handling abrasive materials or navigating complex plant layouts.
Innovations in Design
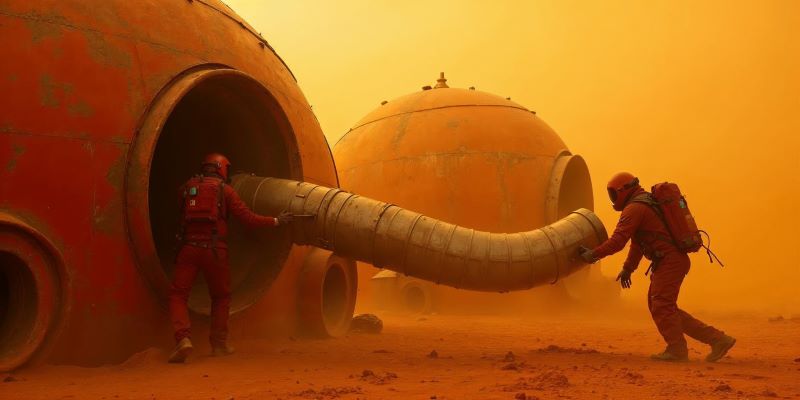
Advances in material science and engineering play a crucial role in the development of custom pneumatic conveyors:
- Wear-Resistant Materials: Utilising ceramics or hardened alloys in areas prone to wear can significantly extend the life of the system.
- Energy-Efficient Components: Incorporating variable frequency drives (VFDs) to control the speed of the air movers according to demand helps reduce energy consumption.
- Modular Design: Modular systems offer flexibility, allowing components to be easily replaced or upgraded as processing needs change or expand.
Software and Automation Enhancements
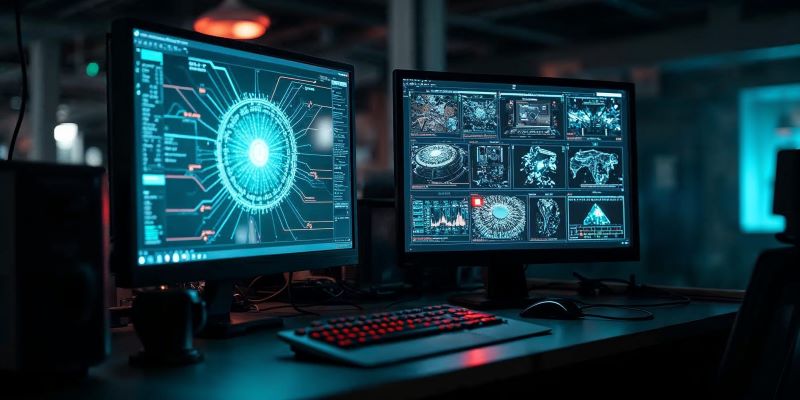
Integration of sophisticated software and automation technologies is key to optimising the performance and reliability of pneumatic conveyors:
- System Control Software: Custom software solutions can automate many aspects of conveyor operation, from adjusting air flow and pressure to monitoring system health, enhancing operational accuracy and reducing downtime.
- Real-Time Monitoring and Diagnostics: Sensors and monitoring systems can detect issues such as blockages, wear, or pressure drops early, facilitating timely maintenance and preventing costly breakdowns.
Selecting the Right Vendor
Choosing the right vendor for a custom-built pneumatic conveyor system is crucial to the success of any industrial project.
The right vendor is a strategic decision that affects not just the procurement and installation phases but the long-term operational efficiency of the pneumatic conveying system. Taking the time to evaluate potential vendors on these criteria will ensure that you partner with a company that can deliver a system tailored to your specific requirements and challenges.
Capt-Air is known for its extensive experience in designing, installing, and maintaining custom pneumatic conveyors for a wide range of clients.
Support and Service
- After-Sales Support: Comprehensive after-sales support, including training, technical assistance, and available spare parts, is essential for the long-term success of your system.
- Maintenance Services: Vendors offering regular maintenance services can help ensure the system operates at peak efficiency and can help prevent unexpected downtime.
Cost Considerations
- Total Cost of Ownership: Consider not just the initial cost but the total cost of ownership, which includes maintenance, energy use, and potential downtime costs. A more expensive system might offer better value over its lifespan due to higher efficiency and lower operational costs.
Case Studies and References
- Proven Success: Request case studies or references from the vendor that demonstrate their capability and success in delivering custom pneumatic conveying systems. This real-world proof can help gauge the effectiveness and suitability of their solutions for your needs.
Experience and
Expertise
- Industry Knowledge: Look for vendors with a proven track record in your specific industry. Their experience with similar materials and environments can provide invaluable insights and a more reliable system.
- Technical Expertise: Assess the technical capabilities of the vendor, including their understanding of advanced pneumatic conveying technologies and their ability to innovate and apply new solutions
Customization Capabilities
- Design Flexibility: Ensure the vendor can offer truly customized solutions that fit your specific operational needs, rather than just adapting standard products.
- Project Management: The ability to manage projects from design through to installation and commissioning is crucial. Effective project management ensures that systems are delivered on time and on budget.
Quality and
Reliability
- Quality Assurance: Check for quality control processes in manufacturing and assembly. Certifications such as ISO can be indicators of a vendor’s commitment to quality.
- System Reliability: Inquire about the reliability of the systems previously installed by the vendor. References or case studies can provide evidence of long-term performance and customer satisfaction.
Conclusions
Custom-built pneumatic conveyors represent a significant investment in the efficiency and safety of industrial operations. Tailored to meet the unique demands of different materials and facility layouts, these systems optimize every aspect of material handling. From enhancing operational efficiency to ensuring compliance with stringent safety standards, the advantages of investing in a custom solution are clear and impactful.
If you’re considering upgrading or implementing a new material handling system, now is the time to explore the benefits of custom-built pneumatic conveyors. Evaluate your current operations, identify potential areas for improvement, and consider how a tailored pneumatic conveying system could enhance your productivity and safety. Reach out to Capt-Air, to provide insights and guidance tailored to your specific needs. Don’t just settle for a standard solution; optimize your material handling processes with a system designed just for you.